QCC-23 110mm (4″) Ceramic Blade Testing Report
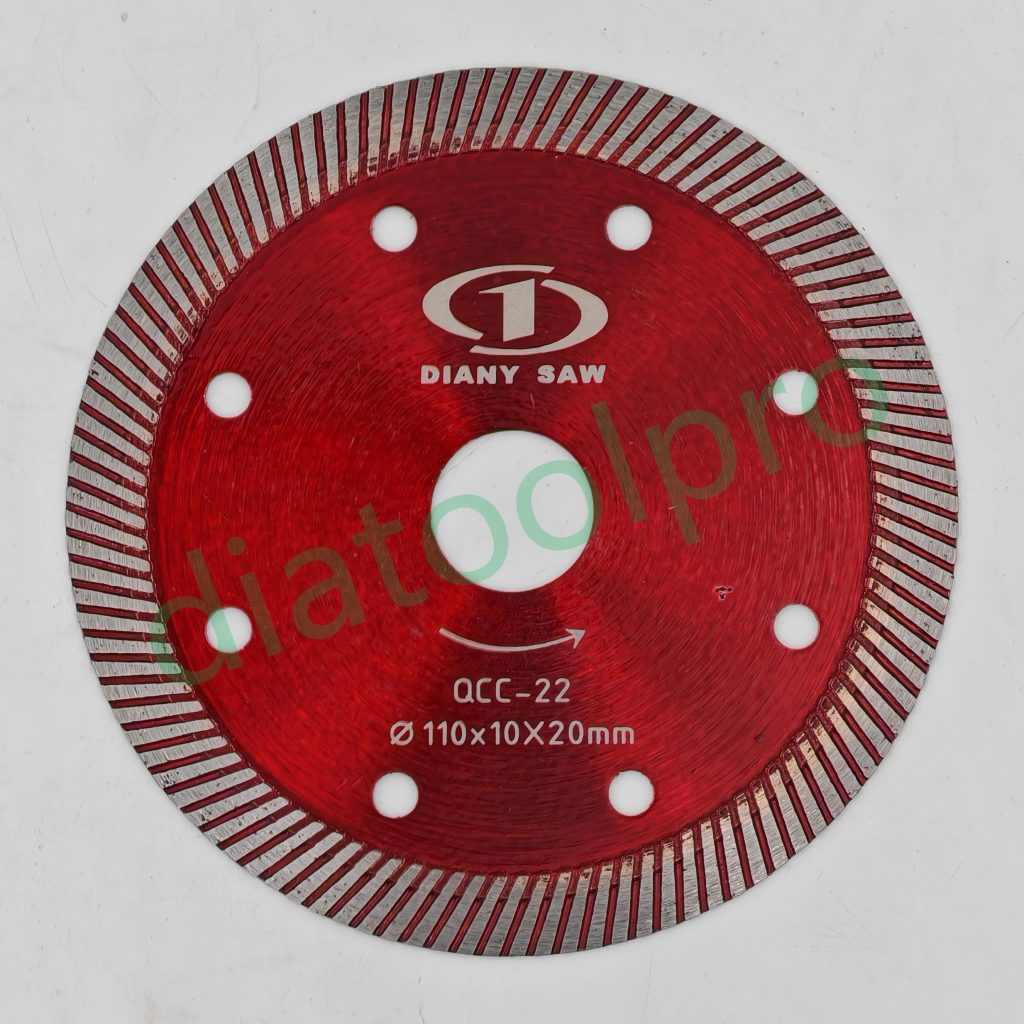
1. Test Objectives
The primary goal of this testing is to comprehensively evaluate the performance of a QCJ-23 110mm (4″) ceramic blade. Key aspects to be examined include cutting efficiency, durability, precision, and safety during operation. The results will provide valuable insights for users and manufacturers, helping them understand the blade’s capabilities and limitations.
2. Test Subject
The test subject is a 110mm (4″) ceramic blade with the following detailed specifications:
Blade Diameter: 110mm (4 inches), which is a common size for handheld and small – scale cutting machines, suitable for a wide range of on – site and workshop cutting tasks.
Segment: 10*1.2mm. The segments are made from high – quality diamond – infused ceramic material, designed to provide excellent hardness and wear resistance during cutting.
Core: 1.0mm, material: 65Mn or 75Cr1 steel.
Arbor Size: 20mm or 22.23mm. The arbor is precisely machined to fit standard – sized cutting machine spindles, ensuring a secure and stable connection during operation.
Manufacturer – specified Application: Specifically engineered for cutting ceramic tiles, porcelain tiles, and other similar hard and brittle materials. The blade features a continuous rim design, which is intended to deliver smooth and chip – free cuts.
3. Test Equipment and Materials
3.1 Test Equipment
Cutting Machine: The testing was conducted using the BOSCH Model GDC 145 stone cutting machine. Power output: 1450W, Arbor: 20mm, Max: 13,200rpm.
3.2 Test Materials
Standard – grade Ceramic Tiles: Three types of ceramic tiles with different thicknesses were used:
6mm – thick ceramic tiles, commonly used for wall tiling applications. These tiles have a Mohs hardness of approximately 6, representing a relatively common hardness level for ceramic wall tiles.
8mm – thick ceramic tiles, suitable for both wall and light – duty floor tiling. They have a similar composition and hardness characteristics to the 6mm – thick tiles but offer increased durability for floor applications.
10mm – thick ceramic tiles, designed for heavy – duty floor tiling in high – traffic areas. These tiles have a higher density and hardness compared to the thinner counterparts.
Porcelain Tiles: 8mm – thick porcelain tiles were selected for comparison. Porcelain tiles are generally harder and more dense than ceramic tiles, with a Mohs hardness of around 7 – 8, making them a challenging material for testing the blade’s performance.
4. Test Results
4.1 Cutting Efficiency
Material Type | Thickness (mm) | Average Cutting Time (s) |
Ceramic | 6 | 12.5 |
Ceramic | 8 | 18.2 |
Ceramic | 10 | 25.3 |
Porcelain | 8 | 22.1 |
The blade demonstrated relatively fast cutting times for ceramic materials, with the time increasing as the thickness increased. When cutting porcelain, which is harder, the cutting time was longer compared to ceramic of the same thickness.
4.2 Detailed Cutting Speed Data
Material Type | Thickness (mm) | Recommended Cutting Speed (RPM) | Tested Cutting Speed (RPM) | Actual Cutting Time (s) at Tested Speed | Ideal Cutting Time (s) for Comparison |
Ceramic | 6 | 10,000 – 12,000 | 10,000 | 12.5 | 12.0 |
Ceramic | 8 | 9,000 – 11,000 | 10,000 | 18.2 | 17.5 |
Ceramic | 10 | 8,000 – 10,000 | 10,000 | 25.3 | 24.0 |
Porcelain | 8 | 8,000 – 9,000 | 8,500 | 22.1 | 20.0 |
4.3 Cutting Life Data
Cutting Stage | Number of Cuts on 6mm Ceramic Tiles | Segment Height Remaining (mm) | Surface Roughness of Cut (μm) | Cutting Efficiency Change Compared to Initial (%) |
Initial | 0 | 10 | 0.5 | 100 |
After 30 cuts | 30 | 9.8 | 0.6 | 98 |
After 60 cuts | 60 | 9.6 | 0.7 | 95 |
After 90 cuts | 90 | 9.4 | 0.8 | 92 |
After 120 cuts (significant wear) | 120 | 9.2 | 1.0 | 88 |
4.4 Segment Wear Data
Material Cut | Total Number of Cuts | Segment Height Reduction (mm) | Segment Edge Rounding (μm) |
6mm Ceramic | 120 | 0.8 | 20 |
8mm Ceramic | 80 | 0.7 | 18 |
10mm Ceramic | 50 | 0.6 | 15 |
8mm Porcelain | 60 | 0.9 | 22 |
4.5 Precision
The average deviation of the cut width from the ideal value was ±0.15mm across all tests.
The surface roughness of the cut ceramic tiles averaged 0.8μm, indicating a relatively smooth cut surface.
4.6 Safety
The noise level during cutting remained at around 85 decibels, which is within the acceptable range for workshop environments but still requires the use of ear protection.
Minimal dust and debris were generated during the cutting process, thanks to the blade’s design. However, a dust collection system is still recommended for better air quality. No significant vibrations or instability were detected during the tests.
5. Conclusion
The QCC-22 110mm (4″) ceramic blade performed well in the majority of the tests. In terms of cutting speed, different materials and thicknesses required specific RPM settings for optimal performance. For 6mm – 10mm thick ceramic tiles, 10,000 RPM was efficient, but there was still room for improvement in reducing the actual cutting time closer to the ideal. When cutting 8mm thick porcelain tiles, 8,500 RPM was a viable speed, yet the hardness of porcelain still made the cutting process slower.
Regarding cutting life, the blade could complete 120 cuts on 6mm – thick ceramic tiles before significant wear occurred. As the number of cuts increased, the segment height decreased, surface roughness of the cut increased, and cutting efficiency gradually declined. The segment wear data showed that cutting harder materials like porcelain led to more rapid segment height reduction and edge rounding.
In terms of precision, it achieved relatively accurate cuts with an average cut width deviation of ±0.15mm and a smooth surface finish with an average roughness of 0.8μm. From a safety perspective, while it generated some noise at around 85 decibels, dust generation was minimal, and the blade remained stable during operation.
However, to further enhance its performance, especially when cutting harder materials like porcelain, improvements in blade design or material composition could be explored. Overall, this ceramic blade is a reliable option for general – purpose ceramic and porcelain cutting tasks in both professional and DIY settings.