What is a “Bond”?
In diamond tool manufacturing, the bond refers to a composite matrix of metal powders (such as copper, tin, bronze, or nickel) carefully engineered in specific proportions to achieve targeted wear rates. This matrix serves a dual purpose:
1. Holding Diamonds Securely: The bond securely anchors diamond particles during cutting, ensuring they withstand the mechanical stresses and friction generated during use.
2. Controlled Wear Mechanism: A properly formulated bond releases worn diamond grit at the optimal time—just as the diamond’s cutting edges become dull or fractured. This process exposes fresh, sharp diamonds from the underlying layer, maintaining consistent cutting efficiency without compromising the blade’s structural integrity.
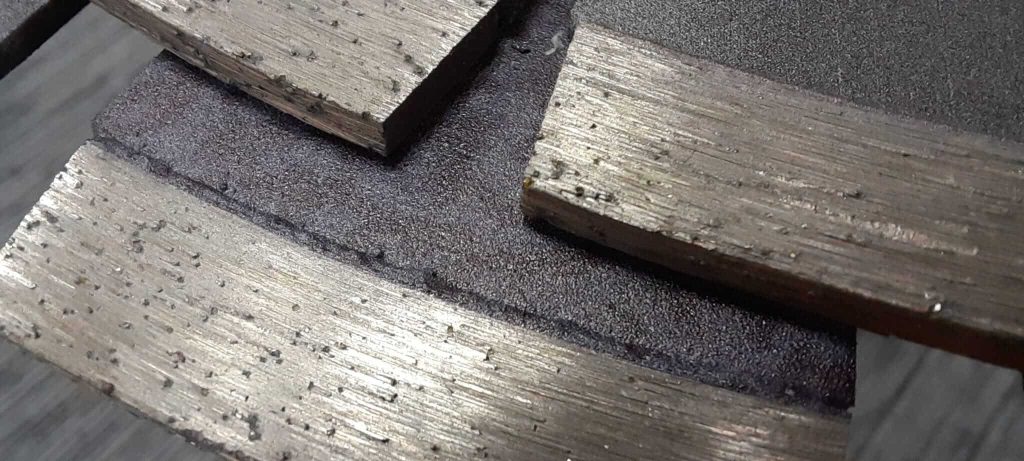
The bond’s composition directly dictates a tool’s performance:
– A softer bond wears faster, ideal for hard materials (e.g., granite) where rapid grit exposure is critical.
– A harder bond wears more slowly, suited for soft, abrasive materials (e.g., asphalt) that require prolonged grit retention.
In essence, the bond acts as both a support structure and a precision wear mechanism, balancing diamond retention and exposure to optimize cutting performance for specific materials and applications.
Most materials can be categorized into the following groups based on their hardness and abrasiveness, each requiring specific diamond blade bond types for optimal performance:
1. Hard Materials
Examples: Granite, clay products, flint concrete, engineering brick.
When cutting hard materials like granite, a soft bond is essential. The soft bond matrix releases diamond grit at the optimal moment of wear, ensuring fresh abrasive particles are continuously exposed. This prevents the bond from retaining dull grit for too long, which would otherwise generate excessive heat, glaze the blade, and halt cutting efficiency.
2. Medium-Hard Materials
Examples: Concrete products, building materials.
For medium-hard materials, a medium-hard bond strikes the ideal balance. It keeps diamond grit sufficiently exposed to maintain cutting aggressiveness while ensuring the bond wears at a controlled rate. This balance maximizes blade life and performance. Most “universal” blades on the market feature a medium-hard bond, making them versatile for general-purpose applications.
3. Soft and Abrasive Materials
Examples: Bricks, blocks, concrete roof tiles.
While these materials are softer than granite or concrete, they often contain abrasive aggregates (e.g., sand, gravel). A medium bond is still preferred here. Though the material itself is less hard, the abrasive nature requires a bond that retains grit long enough to efficiently cut through the matrix without premature wear. Universal medium-bond blades typically handle these materials well, as they avoid the extremes of overly soft or hard bonds that could reduce productivity or cause excessive grit loss.
4. Extremely Abrasive Materials
Examples: Asphalt, low-strength concrete blocks (e.g., 3-Newton blocks).
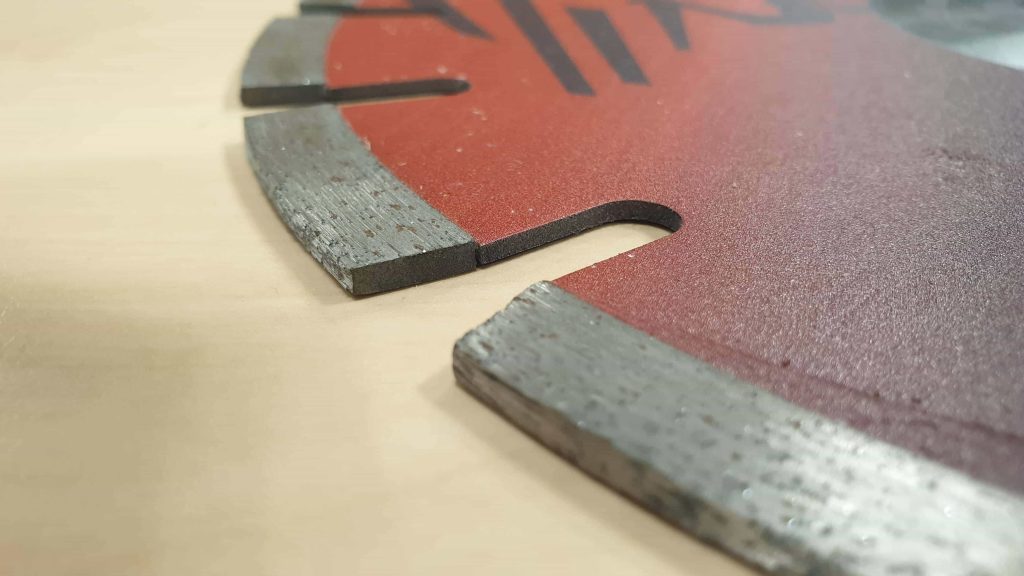
For highly abrasive yet relatively soft materials like asphalt, a hard bond is critical. The hard bond securely holds diamond grit throughout its lifecycle, allowing each particle to fully utilize its cutting potential. Using a soft bond in these applications would cause the matrix to wear too quickly, releasing underequipped grit and wasting valuable diamonds. While a soft bond blade might still cut the material, it would do so inefficiently, with reduced productivity and shorter lifespan.
By aligning blade bond type with material characteristics, users can optimize cutting efficiency, extend blade life, and reduce operational costs.